In the ever-evolving realm of metalworking, the integration of IoT, Industry 4.0, and connected machine monitoring is transforming manufacturing processes. IoT seamlessly links machines, sensors, and devices throughout the metalworking cycle, facilitating the collection, analysis, and transmission of real-time data, ensuring a smooth flow of information across the entire value chain.
This data is channeled to a centralized machine monitoring system, which can promptly identify potential issues or inefficiencies, enabling proactive maintenance and reducing unplanned downtime.
Additionally, staying updated with the latest palladium investing news and metal industry analytics is vital for companies to remain competitive and adapt to market changes. This information offers timely insights into emerging trends and innovations.
Whether a shop is just beginning its digitalization journey or already employing Industry 4.0 solutions, the sheer volume of available technologies and data can be overwhelming. By drawing parallels from the machining industry, shops can better navigate the digital transformation landscape to discover the optimal strategy and technology to enhance their operations.
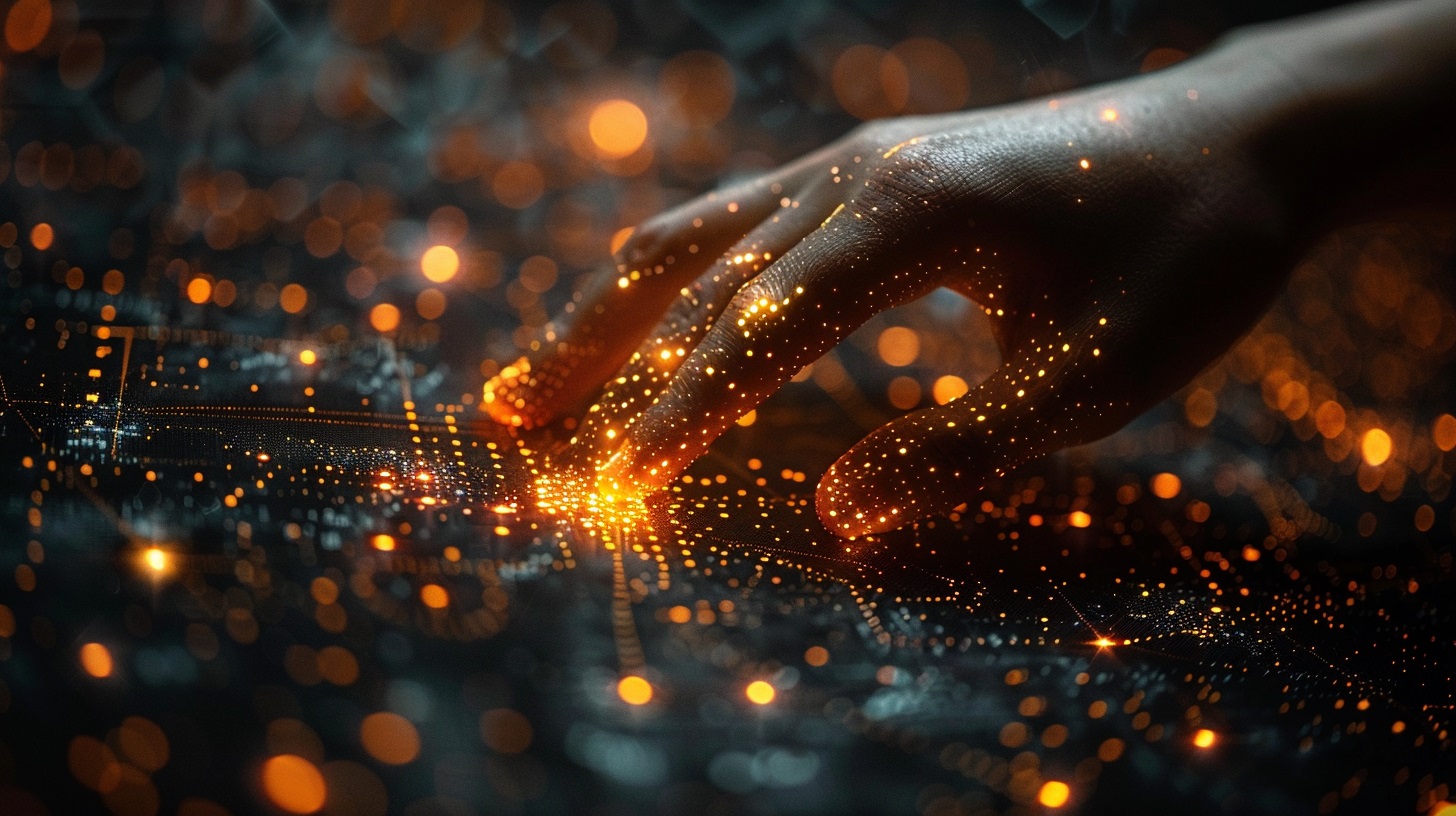
Move beyond the andon lights
Relying just on green, yellow, and red andon lights to show machine status and usage doesn’t make full use of machine data. For example, a red light might mean a machine crash, an engineering test, or there’s no work material.
Some companies use in-house analytics with historical data for insights, but industry-specific machine monitoring systems can give real-time, detailed analytics about what’s really going on behind those lights.
In metal cutting shops, this data is gathered based on rules agreed upon by the condition monitoring software provider and the machining operation, often using industry-standard measurements for overall equipment effectiveness (OEE), which cover machine utilization, availability performance, and production quality.
These platforms gather and report important data for ongoing improvement and lean manufacturing.
Start small and focus
With many machines generating loads of data, it’s crucial to know which data to focus on. Start by using classic lean principles: identify ongoing issues or bottlenecks—like waste, unexpected downtime, or quality problems with certain parts or machines—that need deep data analysis for root cause discovery.
For instance, many shops learn that operators spend more time on setups than actual machining. Users can set up and track things like setup times, part loading/unloading, and changes in fixtures or tools to spot waste and low usage. This real-time data is more accurate for making quick and informed changes to operations or business decisions to hit optimization goals.
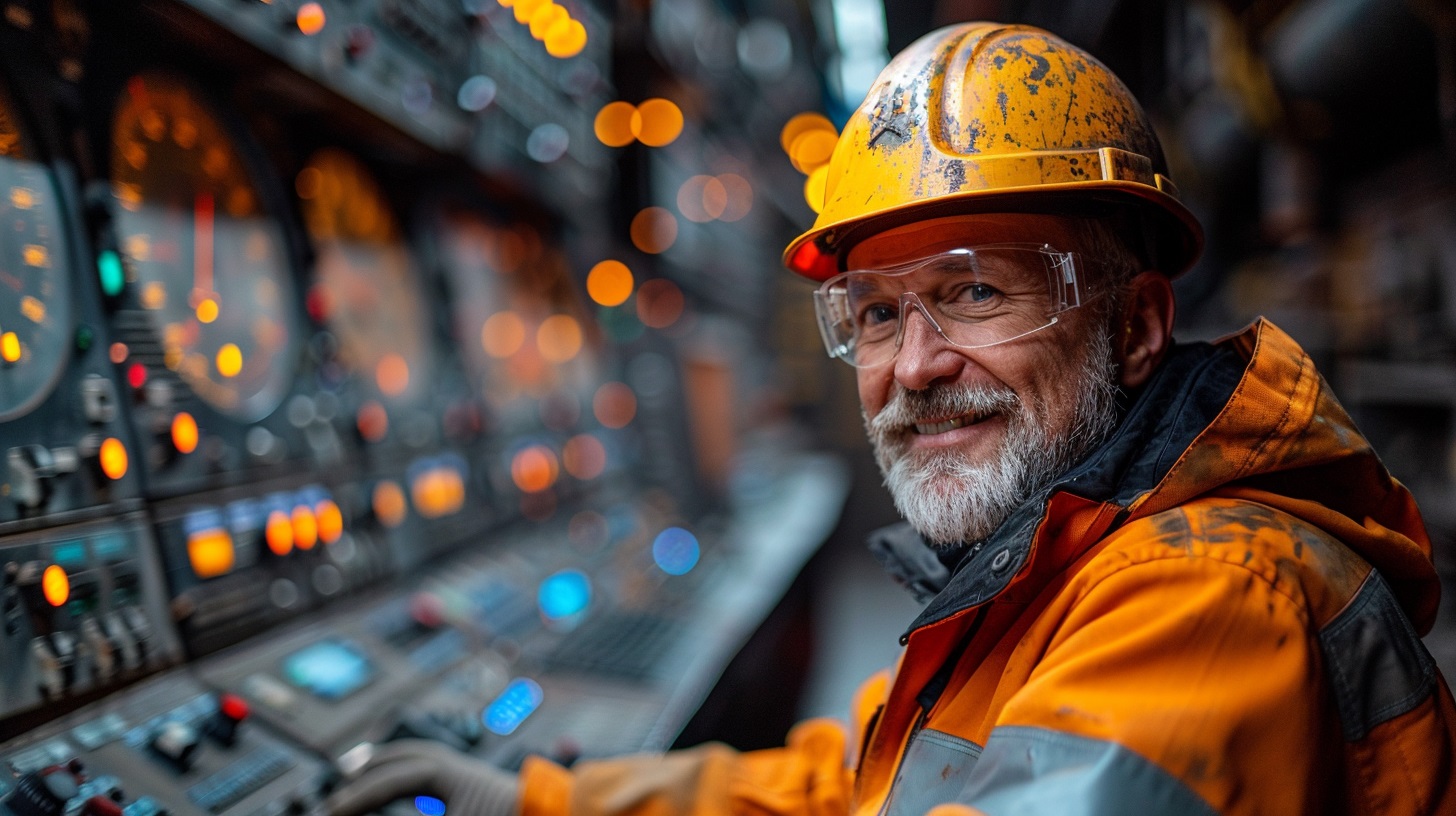
Integrate sensors for actionable insights
In lean manufacturing, using condition monitoring software and on-machine sensors boosts continuous improvement with dynamic data collection. Sensor-enabled tool holders on metal-cutting machines give insights into things like cutting forces and temperature.
This data, sent wirelessly, helps with predictive maintenance by spotting early tool wear and potential failures, avoiding downtime. These smart tools connect with machine PLCs to keep an eye on tool conditions and process stability, using vibration analysis to catch any deviations.
Embrace cloud-based condition monitoring
Cloud-based condition monitoring platforms offer big advantages over traditional systems, providing seamless connectivity and advanced real-time analysis through cloud applications. These platforms let you access machine data globally while keeping it secure with government compliance.
They also lighten IT loads by having providers manage updates, support quick deployment without extra hardware, and enable strong remote support for multiple locations.
Leverage industry expertise
Picking a condition monitoring software platform built by a manufacturer with deep industry knowledge can be super beneficial, especially if they use the platform to improve their operations. Such partners can offer tech support and help guide shops through their digital transformation journeys, speeding up returns on digital machining investments.
Integrating IoT-enabled equipment and machines into a machine monitoring platform gives shops crucial insights to quickly spot and reduce process waste. With trusted expertise and support, shops can boost productivity and, in turn, their business success.